The Definitive Guide to Roar Solutions
The Definitive Guide to Roar Solutions
Blog Article
The Roar Solutions PDFs
Table of Contents6 Simple Techniques For Roar SolutionsThe Facts About Roar Solutions UncoveredThe Only Guide to Roar Solutions
In order to secure installations from a potential surge a method of analysing and identifying a possibly unsafe area is called for. The purpose of this is to ensure the proper selection and installment of devices to inevitably stop an explosion and to guarantee safety of life.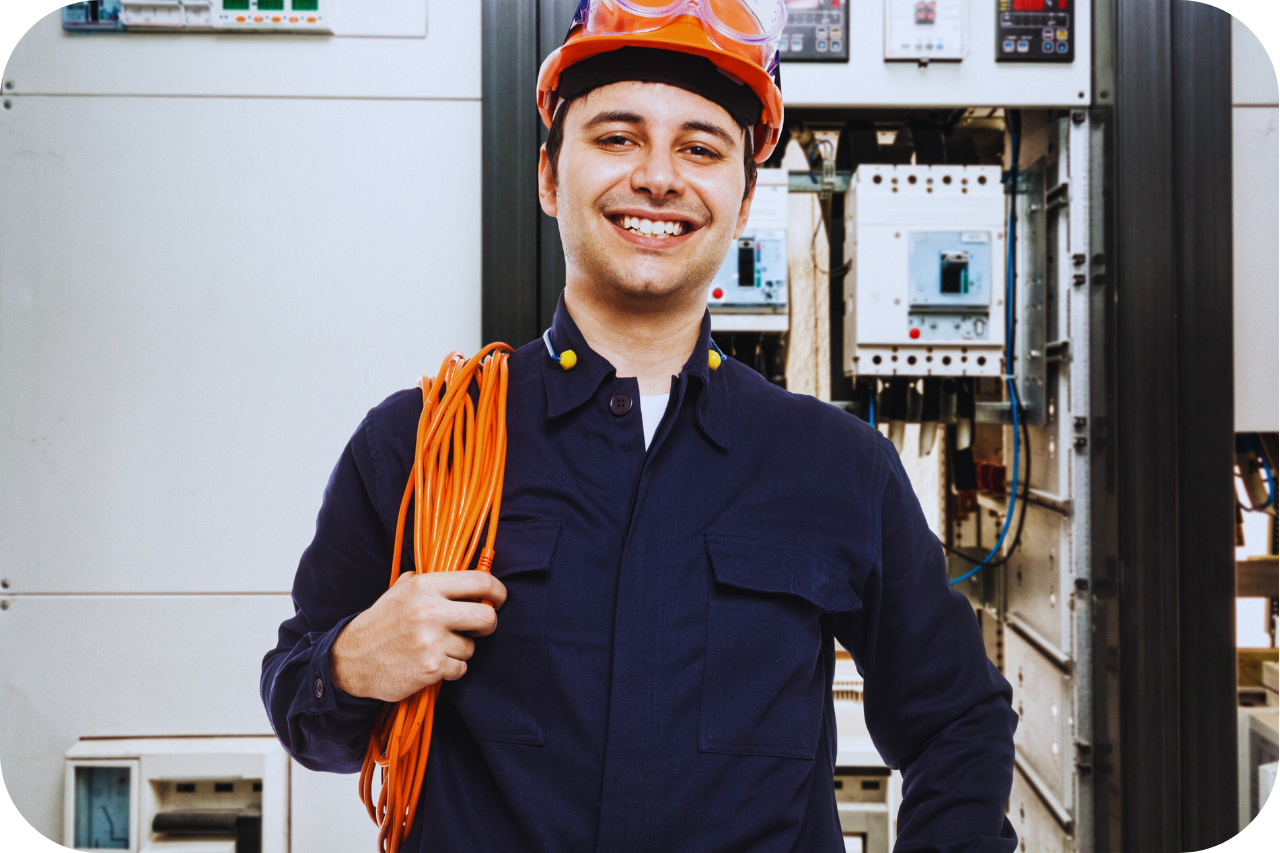
(https://www.4shared.com/u/m0RNXdsL/thomascarrillo4740.html)
No devices must be installed where the surface temperature level of the devices is higher than the ignition temperature of the given hazard. Below are some usual dust dangerous and their minimum ignition temperature. Coal Dust 380C 225C Polythene 420C (thaws) Methyl Cellulose 420C 320C Starch 460C 435C Flour 490C 340C Sugar 490C 460C Grain Dust 510C 300C Phenolic Resin 530C > 450C Aluminium 590C > 450C PVC 700C > 450C Residue 810C 570C The probability of the danger being present in a concentration high enough to cause an ignition will certainly vary from location to place.
In order to identify this danger an installment is divided right into areas of threat depending upon the amount of time the dangerous is existing. These locations are described as Zones. For gases and vapours and dirts and fibers there are 3 zones. Area 0 Area 20 A harmful ambience is very likely to be existing and may exist for lengthy periods of time (> 1000 hours annually) or perhaps continuously Area 1 Area 21 A dangerous atmosphere is feasible yet unlikely to be present for lengthy durations of time (> 10 450 C [842 F] A classification of T6 means the minimum ignition temperature is > 85 C [185 F] Hazardous location electrical tools possibly developed for use in greater ambient temperatures. This would certainly suggested on the score plate e.g. EExe II C T3 Ta + 60C( This means at 60C ambient T3 will certainly not be surpassed) T1 T1, T2, T3, T4, T5, T6 T2 T2, T3, T4, T5, T6 T3 T3, T4, T5, T6 T4 T4, T5, T6 T5 T5, T6 T6 T6 A T Class score of T1 implies the maximum surface area temperature created by the instrument at 40 C is 450 C. Thinking the connected T Course and Temperature level rating for the tools are proper for the area, you can constantly utilize a tool with an extra rigid Division score than required for the location. There isn't a clear solution to this question unfortunately. It really does depend on the sort of devices and what repair work require to be lugged out. Equipment with particular examination procedures that can not be carried out in the field in order to achieve/maintain 3rd party rating. Need to come back to the manufacturing facility if it is before the devices's solution. Area Fixing By Authorised Employee: Complicated screening may not be called for however specific treatments might need to be followed in order for the devices to maintain its third party rating. Authorised employees need to be used to carry out the job correctly Fixing have to be a like for like substitute. New component must be considered as a straight replacement requiring no special screening of the tools after the fixing is complete. Each tool with a hazardous ranking should be examined separately. These are detailed at a high degree below, yet for even more thorough info, please refer straight to the guidelines.
All about Roar Solutions
The tools register is an extensive database of tools records that consists of a minimum set of areas to identify each product's place, technological parameters, Ex lover classification, age, and environmental information. This information is vital for monitoring and managing the devices efficiently within dangerous areas. On the other hand, for regular or RBI tasting examinations, the grade will be a mix of Thorough and Close evaluations. The ratio of Detailed to Close assessments will be determined by the Devices Danger, which is examined based upon ignition threat (the probability of a source of ignition versus the likelihood of a flammable atmosphere )and the harmful location classification
( Area 0, 1, or 2). This variant will additionally affect the resourcing demands for work preparation. As soon as Whole lots are defined, you can create sampling plans based upon the sample size of each Whole lot, which describes the variety of random equipment products to be inspected. To determine the required sample dimension, two facets require to be examined: the dimension of the Lot and the group of inspection, which suggests the degree of initiative that need to be used( reduced, normal, or increased )to the examination of the Whole lot. By combining the group of inspection with the Great deal size, you can then establish the suitable rejection criteria for a sample, suggesting the allowable variety you could try this out of malfunctioning items located within that example. For more information on this procedure, please refer to the Power Institute Guidelines. The IEC 60079 standard recommends that the optimum interval in between inspections need to not exceed three years. EEHA inspections will certainly additionally be performed outside of RBI campaigns as part of set up upkeep and equipment overhauls or repair services. These inspections can be attributed towards the RBI sample dimensions within the impacted Whole lots. EEHA assessments are performed to determine faults in electrical devices. A weighted scoring system is vital, as a solitary piece of equipment might have several faults, each with differing levels of ignition threat. If the consolidated score of both inspections is much less than twice the fault score, the Lot is considered acceptable. If the Great deal is still considered unacceptable, it must go through a complete inspection or validation, which might cause stricter inspection procedures. Accepted Whole lot: The causes of any type of mistakes are determined. If a common failure setting is found, added equipment may call for evaluation and fixing. Faults are identified by seriousness( Safety and security, Integrity, Housekeeping ), making sure that urgent concerns are examined and addressed immediately to minimize any type of influence on safety or operations. The EEHA data source ought to track and tape the lifecycle of mistakes together with the rehabilitative actions taken. Carrying out a durable Risk-Based Inspection( RBI )technique is critical for making certain compliance and security in managing Electrical Devices in Hazardous Areas( EEHA) (eeha training). Automated Mistake Rating and Lifecycle Monitoring: Easily take care of mistakes and track their lifecycle to enhance inspection accuracy. The intro of this assistance for risk-based evaluation even more strengthens Inspectivity's position as a best-in-class solution for regulatory compliance, in addition to for any type of asset-centric evaluation use instance. If you want finding out extra, we invite you to ask for a demonstration and uncover how our solution can transform your EEHA administration processes.
A Biased View of Roar Solutions

In terms of eruptive danger, a hazardous location is a setting in which an eruptive atmosphere exists (or may be expected to be present) in amounts that require unique precautions for the building, setup and use of tools. hazardous area course. In this article we explore the obstacles dealt with in the office, the danger control steps, and the required competencies to work safely
These compounds can, in certain conditions, develop eruptive atmospheres and these can have significant and terrible consequences. Many of us are acquainted with the fire triangular get rid of any type of one of the 3 elements and the fire can not occur, however what does this mean in the context of harmful locations?
In the majority of circumstances, we can do little regarding the degrees of oxygen airborne, but we can have significant impact on resources of ignition, as an example electrical tools. Harmful areas are documented on the dangerous area classification illustration and are recognized on-site by the triangular "EX LOVER" indicator. Here, amongst other essential details, zones are split into three types relying on the threat, the likelihood and period that an explosive atmosphere will exist; Zone 0 or 20 is regarded the most dangerous and Area 2 or 22 is regarded the least.
Report this page